Processing technology for resins using the cryogenic energy of liquefied natural gas
Cryogenic and Freezer Grinding of Resins using liquefied nitrogen
Drying of resins using dry air with low dew point
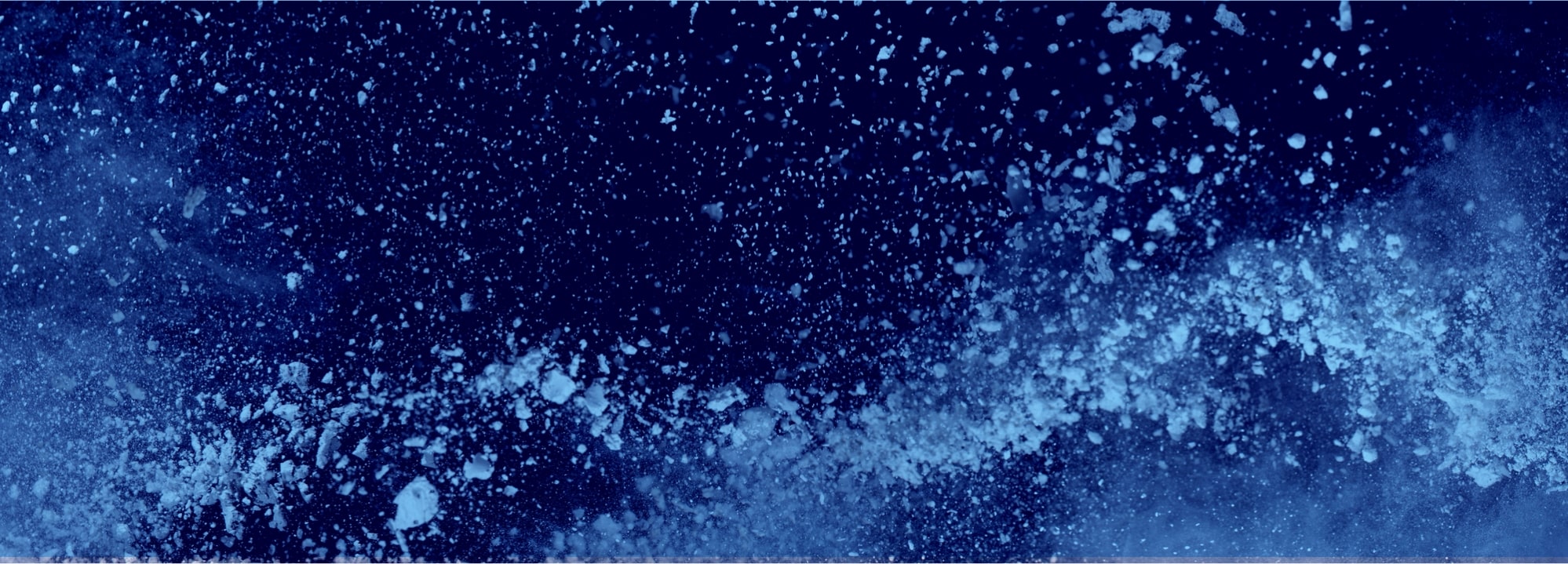
Contract grinding and drying of resins
We are engaged in low-cost and high-efficiency cryogenic and freezer grinding using liquefied nitrogen and drying using dry air with low dew point.
-
Contract grinding of resinsWe grind various resins supplied to us to the desired particle size by cryogenic and freezer grinding using liquefied nitrogen.
-
Contract drying of resinsWe dry various resin pellets supplied to us to the desired moisture content using dry air with low dew point.
Contract grinding of resins
Do you have any problems with procuring resin powder?
-
1
Raw material manufacturers do not deal in the grade of powder that meets your desired performance.
-
2
It is difficult to achieve the target particle size.
-
3
We are worried about investment risk and management burden.
Introduction of expensive equipment, including grinders and liquefied nitrogen tanks, and obligation to assign qualified personnel.
Everything can be solved by outsourcing.
It is also effective from a BCP perspective.We own a variety of grinders and can easily accommodate changes in quantity. We undertake contract grinding under a thorough management system.
Advantage of cryogenic and freezer grinding at Osaka Gas Liquid
We can grind materials that are difficult to pulverize,including super engineering plastics,elastomers and low-melting-point waxes.
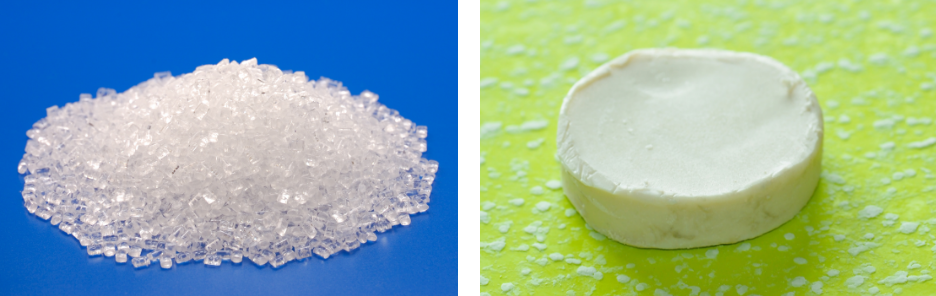
① Finer powder can be obtained.
② The material can be ground without melting it.
③ The low temperatures cause embrittlement of the material,
resulting in efficient pulverization.
We can produce powder with minimal degradation that maintains the characteristics of the raw material before grinding.
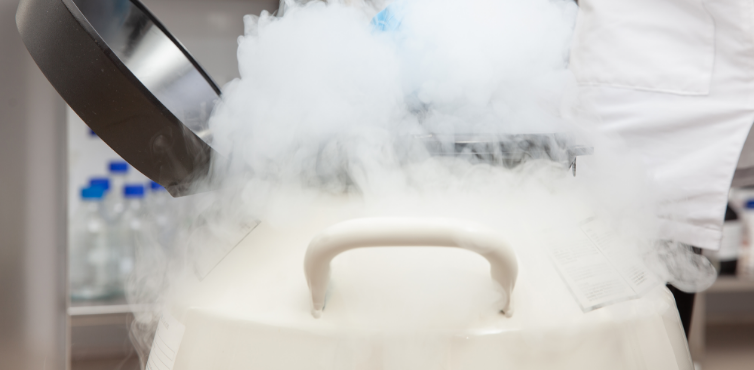
We can control grinding particle size.
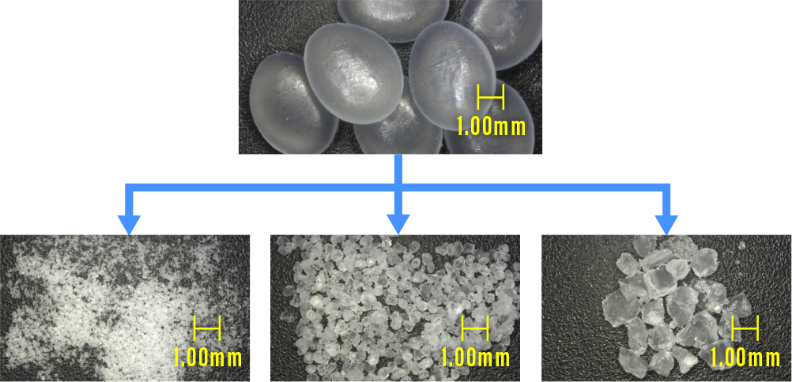
e.g. 200 μm for average particle diameter and 1000 μm for maximum particle diameter.
Main applications
Below are some examples of applications of our ground products.
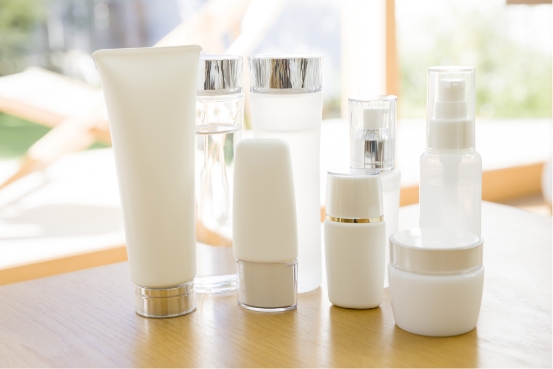
Cosmetics
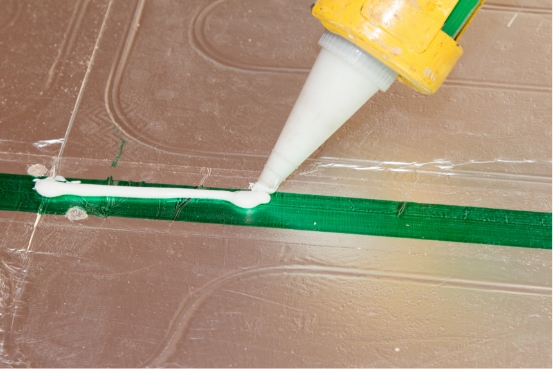
Adhesive
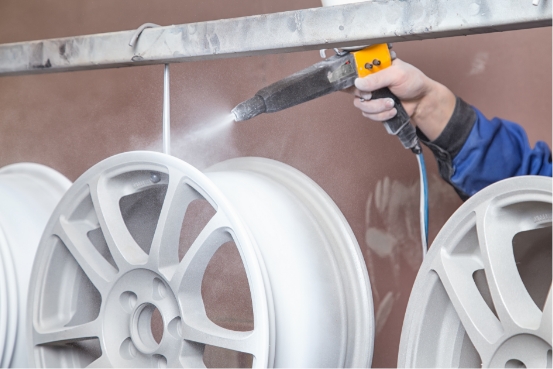
Powder coating
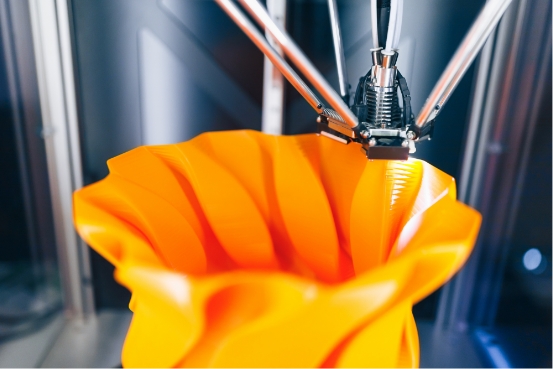
3D printer
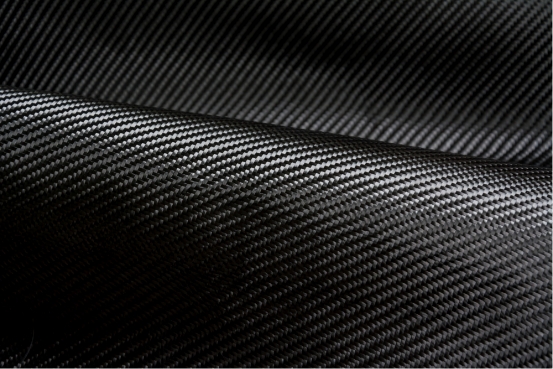
Carbon fiber composite materials
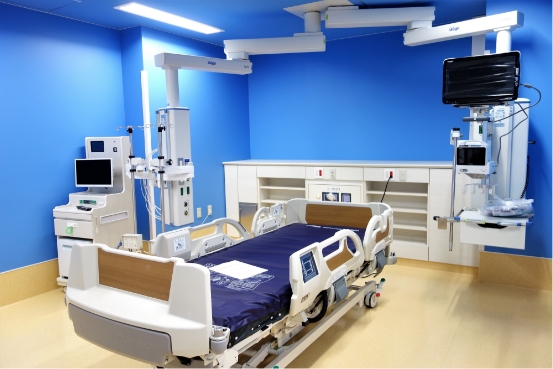
Medical equipment
Flow of grinding resins
By adjusting the internal residence time in the grinder, the material can be adjusted to any desired particle size.
- Cryogenic grinding
- Bringing to room temperature While avoiding moisture absorption
- Classification
- Finish
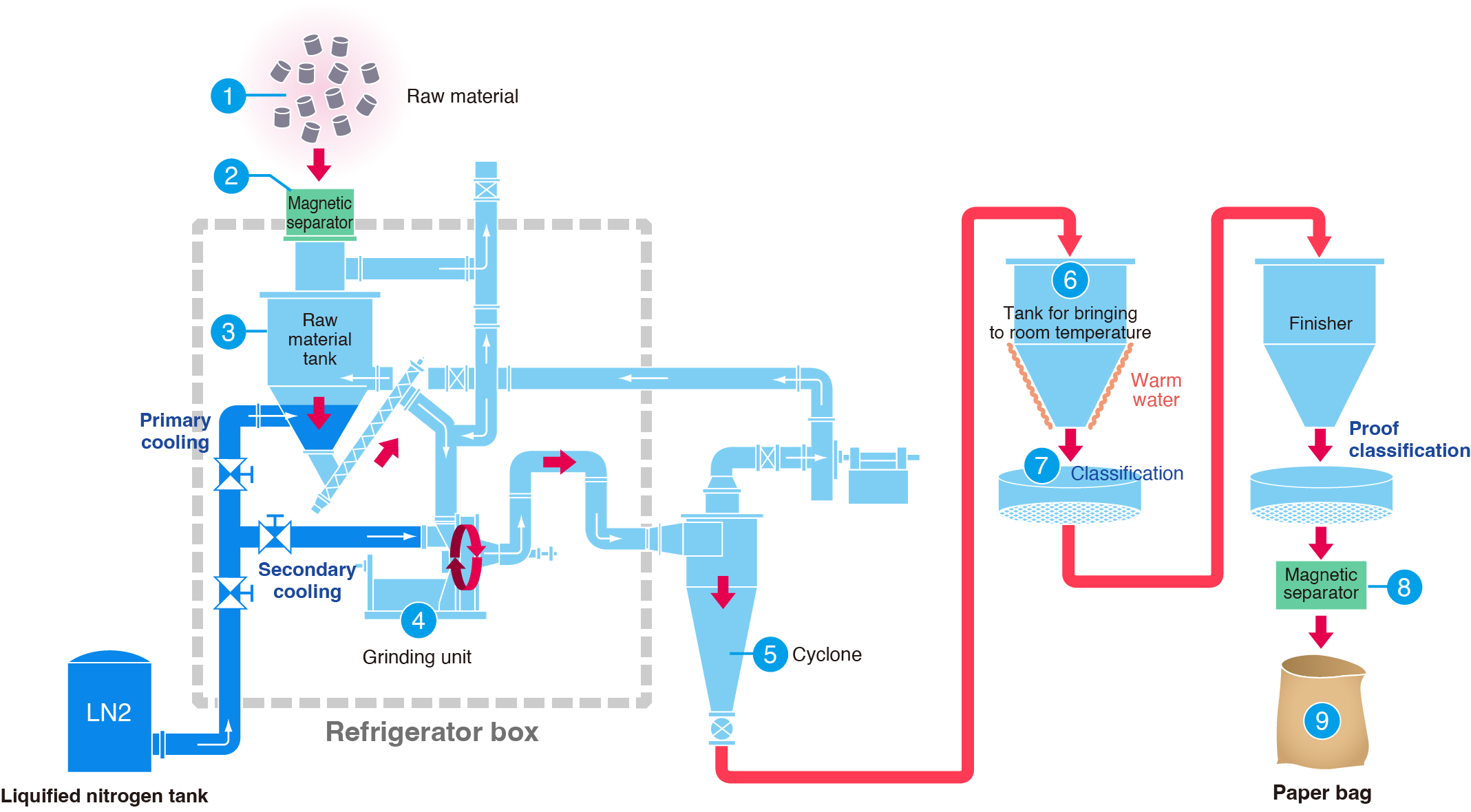
- A wide range of raw materials can be fed, from pellets of approximately 5 mm square to powdered materials.
- Metal foreign matter contained in the raw material is removed using a magnetic separator.
- Resin is fed in the raw material tank filled with liquefied nitrogen in advance and cooled below the brittle point.
- The resin is ground in the grinding unit while the temperature is maintained. The particle size is controlled by grinding conditions.
- Resin that has been ground is collected by centrifugal separation.
- The collected resin is brought to room temperature while avoiding moisture absorption.
- The ground resin is classified to adjust the particle size of the ground product. What remains in the screen is reground.
- Metallic foreign matter is removed from the product by a magnetic separator.
- The product is packaged in our standard* or your specified paper bag.
One lot of products can be produced in a single production run using the continuous production system.
* Paper bag with PE inner bag or aluminum laminate inner bag is standard.
Classification system
We use various types of classifiers to adjust the particle size distribution and add value to the product in terms of quality and performance.
Classification is performed according to the purpose, from testing to mass production.
Classifiers owned and classification points
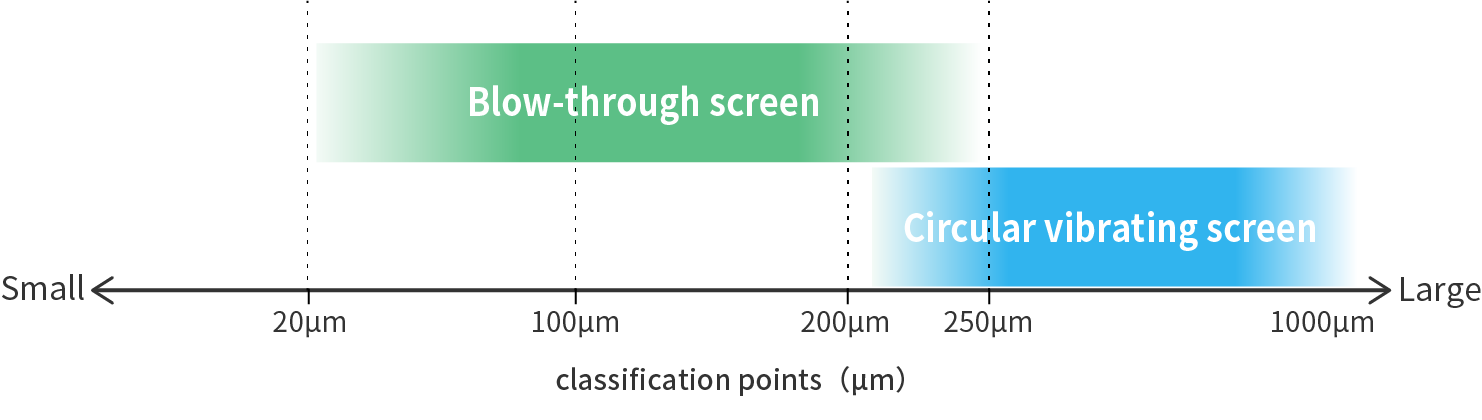
-
Blow-through screen
This performs continuous and efficient classification while preventing mesh clogging by backwash air.
-
Circular vibrating screen
This efficiently screens the product by means of vibration of the mesh surface and horizontal, vertical and inclined movement (three-dimensional movement).
Flow of contract grinding
Our staff members, who are well versed in resin grinding, are ready to respond to your needs
by envisioning products that meet their requirements.
-
First meeting
-
We will listen to your requirements, including the particle size and required quantity, and propose efficient trial grinding.
-
Trial grinding
-
We will conduct trial grinding with small amounts of raw materials (1 to several tens of kilograms) to confirm that the desired powder can be produced.
-
[Customer] Evaluation of prototypes
[Osaka Gas Liquid] Proposal of approximate grinding cost
-
You will evaluate the prototypes.
We will propose a rough estimate of the grinding cost for mass production, taking into account future order status.
-
Meeting for mass production
-
We will discuss the details of mass production, including the specification.
-
To mass production
-
Start of contract grinding
Track record in cryogenic and freezer grinding
Contract drying of resins
Is that drying process a bottleneck for you?
We will help to reduce your workload and improve production by undertaking the drying process.
Advantage of contract drying of resins
-
Minimizing material degradation
We dry materials with minimum degradation due to heat and other factors by adopting dehumidification using dry air with low dew point. -
Minimizing blocking and chipping
We minimize blocking and pellet chipping by using a high-efficiency agitator to minimize agitation required. -
Drying up to several hundred ppm at once
The large 1,000-liter capacity equipment dries the material with several percent moisture content down to several hundred ppm at once.
Dehumidification process using air with low dew point
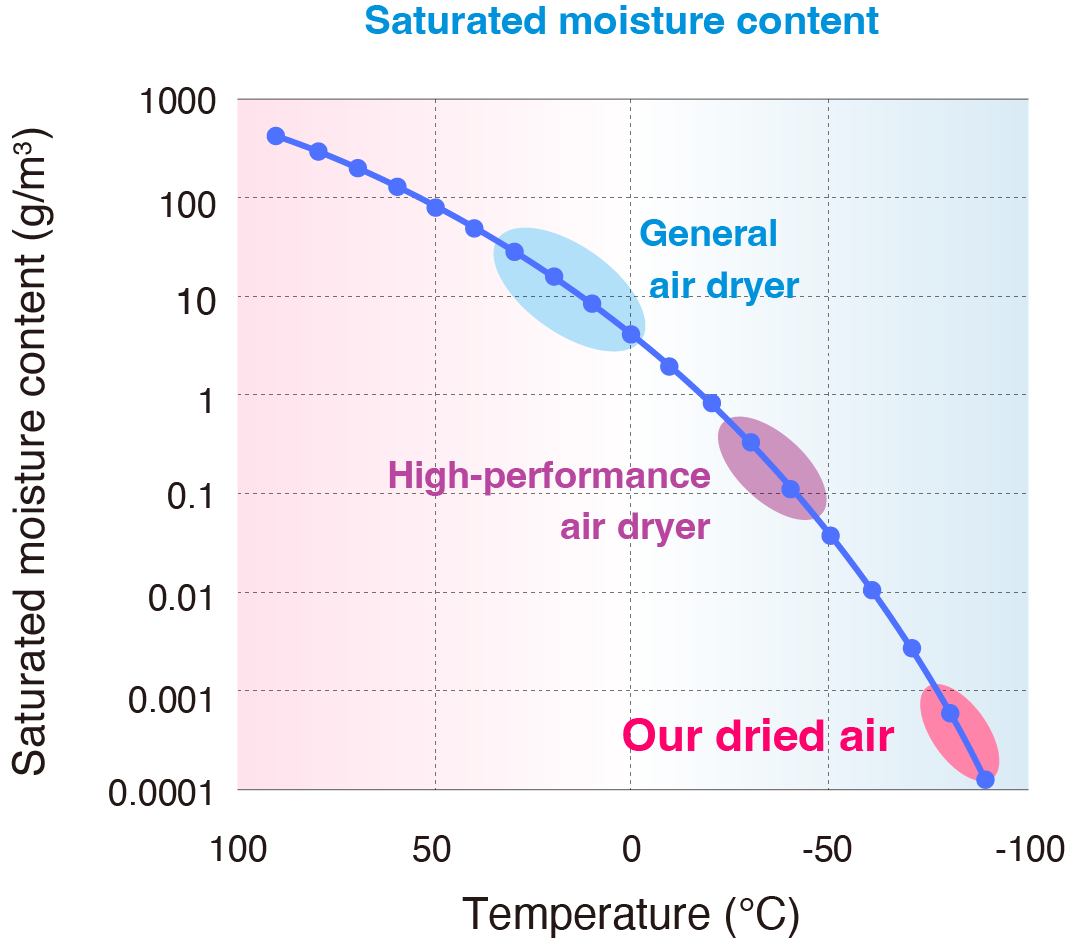


Details of the drying process
item | Description | |
---|---|---|
1 | Packing type of raw material to be fed | Flexible container bag or paper bag |
2 | Packing type of product | Paper bag (our standard* or supplied paper bag) * Paper bag with PE inner bag or aluminum laminate inner bag |
3 | Shape of raw material | Pellets only (in a flexible container or paper bag with a capacity of 750 kg or less) |
4 | Lot size | 500 to 750 kg/batch at minimum |
5 | Drying method | Dehumidification using dry air with low dew point and supplemental heating using hot water |
6 | Product analysis method | Karl Fischer moisture meter |
Examples of materials
-
Polyester
-
Polyurethane
-
Polyamide (Nylon)
Cryogenic Grinding Center
“Resin Factory.”
The factory is equipped with a series of powder processing equipment, including LINREX MILL, and various analytical instruments.
We have extensive experience and superior technology to meet all your needs for grinding, drying, classifying and mixing.
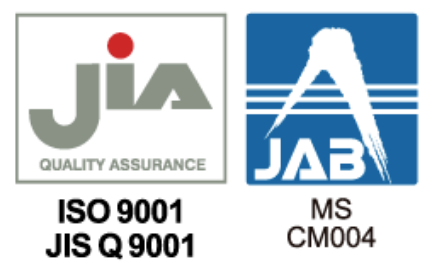
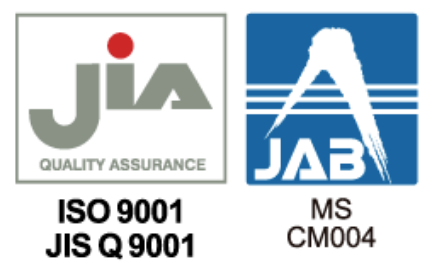
ISO 9001 is an international standard for quality management systems (QMS)
established by the International Organization for Standardization (ISO).
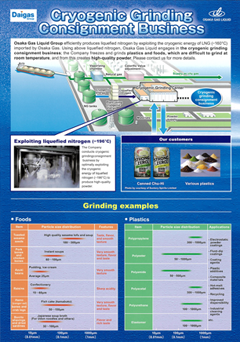
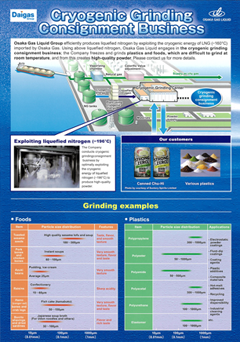
Cryogenic and freezer grinding brochure
Click here to downloadFrequently asked questions
What kind of materials can be ground?
How finely can the material be ground?
What kind of materials can be dried?
What happens if materials do not dry?
② Moisture content evaporates during the molding process in which heat is applied, causing wrinkles, pinholes and/or cavities and thereby leading to reduction in strength and optical properties.